Answering the growing call for environmentally-friendly concrete construction
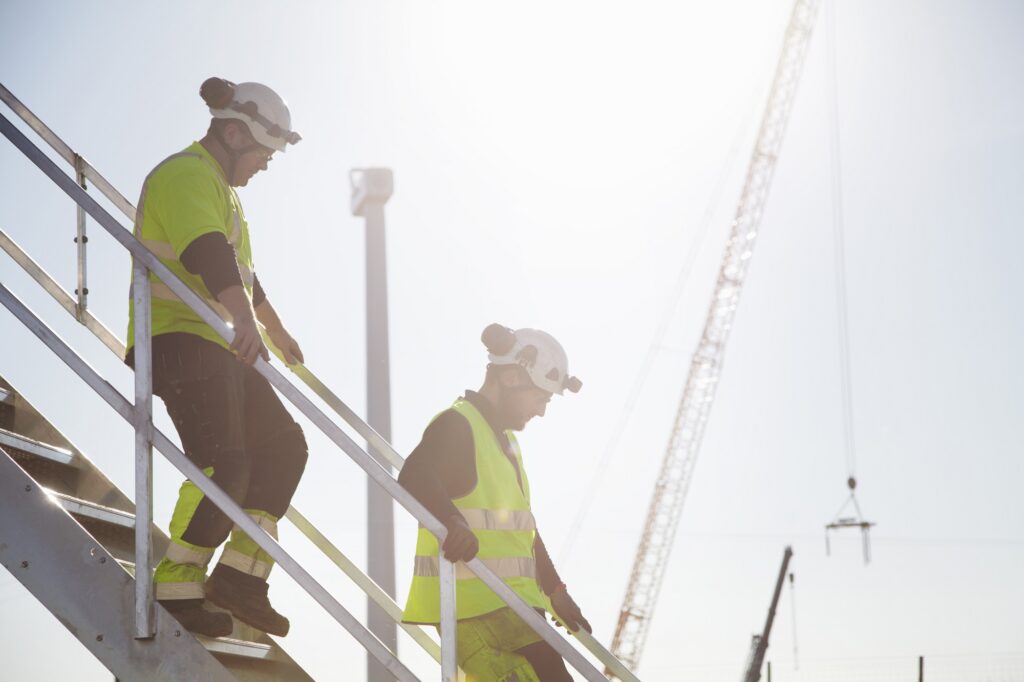
Sustainable practices yield big savings for ready-mix producers
Cement production is the most energy-intensive of all manufacturing industries, according to the U.S. Energy Information Administration. Cement is the main ingredient in concrete, and in the production process, high levels of CO2 are emitted into the air. As limestone is heated to produce cement, it breaks down into calcium oxide and CO2. More emissions are produced by burning fossil fuels to heat the kilns used in cement production.
New approaches to save energy and money
Until now, the only way to produce high flow concrete without segregation was to use a higher cement content and a higher ratio of fine to course aggregates, as is the case with self-consolidating concrete. Fortunately, emerging technologies like control flow concrete are offering new high flowing concrete options to the industry Chryso promotes this new category of high flowing and segregation resistant concrete that utilizes the same conventional mix designs. There is no change in cement content or increased water in the mix to make it flow. Producing and using this type of concrete reduces the overall negative environmental impact as compared to conventional or self-consolidating concrete.
Ready-mix producers aren’t using control flow concrete for altruistic reasons alone. There are many operational and financial benefits to consider:
- Lower material costs. Having lower cement contents saves a lot of money. In addition, producing control flow concrete is easier and more cost-effective than producing self-consolidating concrete, since it uses a conventional mix design.
- Simplify operations. Since control flow concrete can be produced with conventional mix designs and aggregates, it is very simple and has minimal impact to operations when high flow concrete is required for a project.
- Achieve higher margins. By using specially-formulated concrete admixtures in the ready mix concrete production process, ready-mix producers can differentiate themselves by offering contractors higher performance concrete—resulting in more project wins and revenue.
- Reduce chargebacks. Using products like CONCERA® admixtures to produce control flow concrete ensures the consistency of the mix and the production of high quality concrete. No extra water is needed to increase the flow.
- Turn over trucks quickly. control flow concrete flows easily, so there’s faster discharge from the truck. This means ready-mix producers can turnaround trucks faster and deliver more truckloads in a day.
- Preserve equipment. Transporting heavy, sticky conventional concrete can put a lot of strain on the vehicles themselves, not to mention the impact it has on the drum when you need to chip out excess concrete. control flow concrete flows much more easily. This reduces wear and tear and helps extend the life of the fleet.