Calculating Concrete Mix Proportions for FORCE® 10,000D Concrete – TB-0704
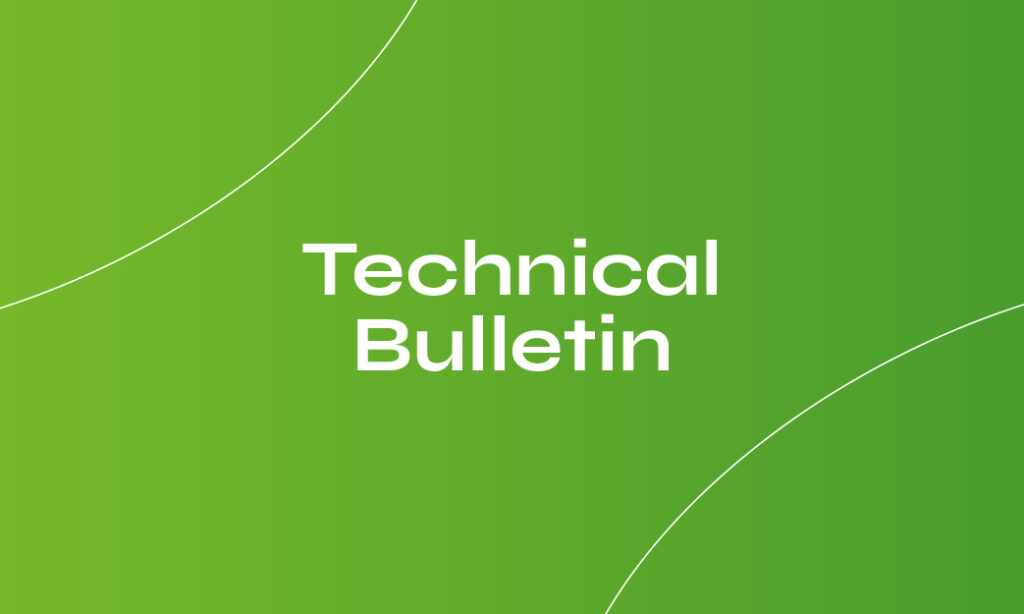
This technical bulletin describes the steps required to adjust concrete mix proportions to accommodate the addition of FORCE 10,000D® dry-densified silica fume.
Specifications
The mix design process begins with a specification which may appear in several forms:
- Prescription Specification–The specifier prescribes that a certain percentage of silica fume be used in the mix; e.g., 7.0% ± 0.5% silica fume by weight of cement. In this specification process, the amount of silica fume required is easy to determine since it is based on a percentage of the amount of cement in the mix design. FORCE 10,000 D®–The calculation is direct, i.e., 7% of 445 kg/m3 (750 lbs/yd3) of cement is 31.2 kg/m3 (52.5 lbs/yd3) of FORCE 10,000 D®.
- Performance Specification–The specifier requires the concrete to have certain properties at a given age; e.g., “the concrete shall pass 1,000 coulombs or less at 90 days by ASTM C1202-94 (AASHTO T277),” or “the concrete shall have a minimum compressive strength of 70 MPa (10,000 psi) at 90 days.” In a performance specification, test mixes must be run to determine the silica fume dosage necessary to meet the coulomb or strength requirements.
- All mix designs must be tested before project start-up to ensure that the FORCE 10,000 D® concrete meets all of the performance requirements for the project. Job site conditions, such as weather, placement procedures and logistics should be anticipated and planned when the mix design is being evaluated prior to project start-up. Please Note: ASTM C1202 (AASHTO T277) should be used as an indicator only. It has a high degree of error and the 90 day testing requirement may create problems. This test method should not be used as a standard for payment penalties.
- Combination Specification–The third type of specification combines both prescription and performance requirements. The specifier requires a certain performance level and a minimum silica fume content; e.g., “the concrete shall have a maximum coulomb reading of 1,000 coulombs at 90 days, and the concrete shall have a minimum silica fume content of 7.5% by weight of cement.” Maximum water/cement ratios, other admixtures and minimum cement factors may also be specified.
Part 1: FORCE 10,000 D® — Dry-densified Silica Fume
A concrete producer wants to use FORCE 10,000 D® to meet a specific requirement of 1,000 coulombs at 28 days. The specification also calls for a maximum water/cement ratio of 0.40. The producer plans to use 7.5% silica fume by weight of cement to meet this coulomb requirement. Concrete workability must also be taken into consideration.
Part 2: Concrete Mix Adjustments
Testing the concrete mix prior to the job start-up provides a performance history for the mix and allows adjustments that may be necessary to meet project requirements. These adjustments may include the following:
- Increasing the Silica Fume Dosage—Silica fume dosage rates have to be adjusted upward to meet the performance requirements for a particular project.
- Increasing the Superplasticizer Dosage—The addition of silica fume to concrete increases the cohesiveness of the mix and additional superplasticizer is normally required to provide the required workability.
- Increasing the Air-Entraining Agent Dosage—The addition of silica fume to concrete may decrease the efficiency of the air-entraining agent. If this occurs, adjust the air-entraining agent dosage rates upward.
Step 1:
Start with a mix that meets the water/cement ratio requirement.
Materials | SSD Mass, kg/m3 | SSD Weight, lbs/yd3 |
---|---|---|
Cement | 386 | 650 |
Water | 154 | 260 |
W/C | 0.40 | 0.40 |
Fine aggregate (SG-2.65) | 712 | 1200 |
Coarse aggregate | 1068 | 1800 |
ADVA® | 261 mL/100kg | 4 oz/100 lbs |
Air content | 6.5% | 6.5% |
Step 2:
Convert 7.5% silica fume to kg (lbs) based on the cement factor.
- Silicia Fume (SG=2.20): 386 kg X 7.5%=29 KG 650 lbs X 7.5%-49 lbs
Step 3:
Adjust the yield of the mix to account for the addition of the silica fume.
|
Step 4:
Adjust the amount of superplasticizer to maintain the same workability as the original mix. The amount of superplasticizer needed varies from job to job depending upon the materials used in the mix and the placement conditions.
Unit of Measurement | SI | US |
---|---|---|
Original ADVA® dosage | 261 mL/100 kg cement | 4.0 oz/100 lbs cement |
Added ADVA® dosage to compensate for addition of FORCE 10,000® | 261 mL/100 kg cement | 4.0 oz/100 lbs cement |
Total ADVA® dosage | 552 mL/100 kg cement | 8.0 oz/100 lbs cement |
Step 5:
Recalculate the mix design for the addition of FORCE 10,000 D®, dry-densified silica fume with the addition of ADVA®.
Materials | SSD Mass, kg/m3 | SSD Weight, lbs/yd3 |
---|---|---|
Cement | 386 | 650 |
Water | 154 | 260 |
W/C | 0.40 | 0.40 |
Fine aggregate | 712-35=677 | 1200-59=1141 |
Coarse aggregate | 1068 | 1800 |
ADVA® | 552 mL/100kg | 8 oz/100 lbs |
Air content | 6.5% | 6.5% |
FORCE® 10,000 D | 29 | 49 |
Step 6:
Run a test on the mix to assure that it meets all project requirements prior to start of the job.