Recommendations Regarding Joint Fillers
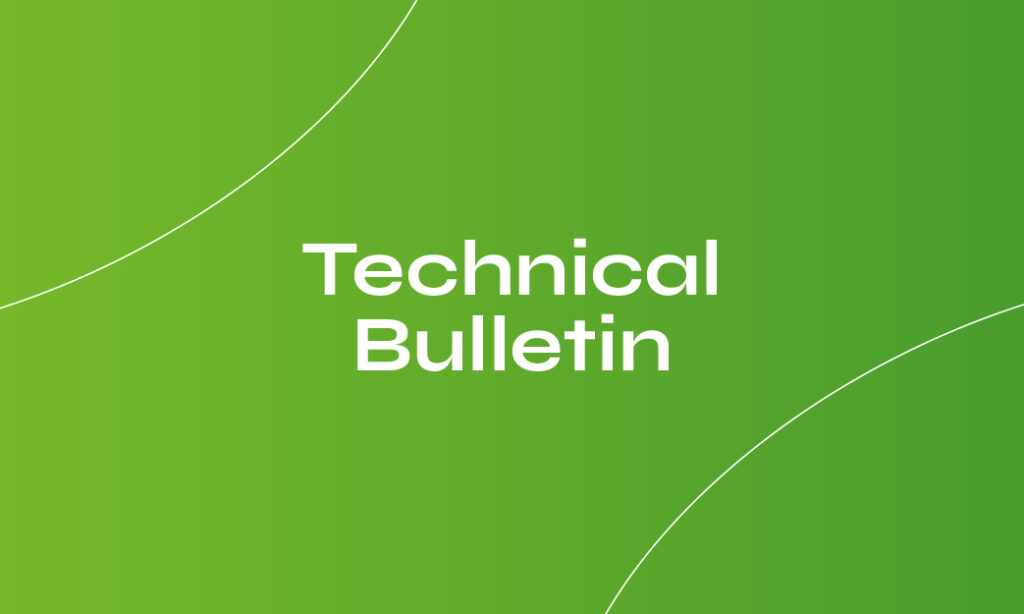
DEFER JOINT FILLING AS LONG AS POSSIBLE TO MINIMIZE THE EFFECTS OF “DRYING SHRINKAGE RELATED JOINT OPENING” ON THE JOINT FILLER
Earlier filling will result in greater separation due to normal drying shrinkage of the concrete, thus increasing the required maintenance. If the joint should be filled before most of the floors expected drying shrinkage has occurred (1 to 1.5 years), separation should be expected between the joint shoulder’s edges and the joint filler or within the joint filler itself.
DEFER JOINT FILLING OF CLIMATE CONTROLLED FACILITIES UNTIL HVAC UNITS ARE OPERATIONAL AND/OR THE BUILDING IS AT OPERATING TEMPERATURE
Submit freezer temperature draw down plans to the SEOR for approval. Maintain the controlled temperatures for two (2) weeks minimum prior to filling the joints.
FILL JOINTS ON FLOORS THAT ARE EXPOSED TO AMBIENT TEMPERATURES WHEN THE BUILDING IS AT ITS “ANNUAL MEAN TEMPERATURE”
For best filler performance of floors that are exposed to ambient temperatures, fill the joints when the building is at its “Annual mean temperature”.
Calculating Annual Mean Temperature – Add the mean monthly temperatures for the months of the calendar year, January to December, together, and then divide by 12.
HOLD A MEETING WITH THE FILLER INSTALLER / MAINTENANCE CONTRACTOR
Prior to the commencement of the joint filling installation work, hold a meeting with the Joint Fill Contractor to determine which filler product, Polyurea or Epoxy, would perform the best under the project conditions and facilitate future filler maintenance. Also, at this meeting, determine who will be responsible for joint filler maintenance after the initial installation. Recommendations are not intended to modify the warranty in any way unless otherwise explicitly stated.
PRODUCTS AND INSTALLATION
Products and Installation conform with manufacturers’ instruction, meeting or exceed the joint filling criteria established in the latest ACI 302 and ACI 360 Committee published documents
ACI 302 – 7.8—Joint materials Properties
PROPERTY | TEST METHOD | PROPERTY VALUE |
Shore A Hardness | ASTM D2240 | ≥ 90 |
Solids Content | 100% |