STRUX® 90/40 Concrete Recommended Mix Designs, Dispensing, Mixing, Placing and Finishing – TB-1200
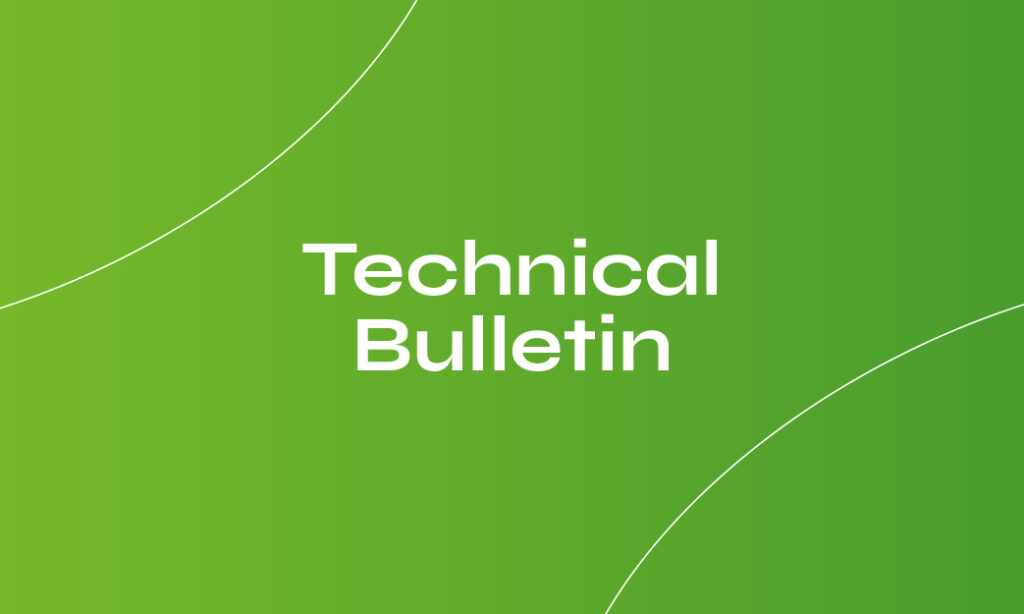
STRUX® 90/40 Synthetic Macro Fiber Reinforcement is a 40 mm (1.55 in.) long high strength and high modulus synthetic macro reinforcement that provides toughness, impact and fatigue resistance to concrete. Primary applications for STRUX® 90/40 at typical dosage rates of 1.8 to 7.0 kg/m3 (3.0 to 11.8 lbs/yd3) include commercial, industrial and residential flooring and other flatwork. Often, slight mix design adjustments and dispensing, placing and finishing modifications are required, especially when higher addition rates of STRUX® 90/40 are used. Batching, mixing, delivering and sampling of STRUX® 90/40 reinforced concrete should be done in accordance with the recommendations detailed below along with applicable sections of ACI 304 (Guide for Measuring, Mixing, Transporting and Placing Concrete) and ASTM C1116 (Fiber-Reinforced Concrete and Shotcrete).
STRUX® 90/40 Mix Proportioning
In some cases, standard 20–30 MPa (3,000–4,500 lbs/in.2) slab on grade mix designs require no or minimal adjustments to accommodate the inclusion of STRUX® 90/40. However, slight mix design changes as detailed below will assure STRUX® 90/40 concrete can be easily handled during the batching, mixing, pumping, placing and finishing processes.
- The surface area of STRUX® 90/40 fibers consumes a percentage of the mortar fraction (cement/sand/water), thereby reducing the workability of the mix. This mortar fraction loss may make an unmodified mix appear and finish “rocky”, while finishers typically prefer a “creamy” finishing mix. Therefore, as detailed in ACI 544.3, it is recommended mix designs be modified to include a maximum 55% by volume coarse aggregate content by total volume of aggregates (sand and stone). As STRUX® 90/40 dosage rates increase, this modification will become more critical to assure that an adequate mortar fraction is available. In some cases, slight increases (up to 30 kg/m3; 50 lbs/yd3) in cementitious contents may also be required to restore a satisfactory mortar fraction.
- The inclusion of STRUX® 90/40 in a mix design normally results in a reduction in slump of approximately 25 mm (1 in.) for every 1.2 to 1.8 kg/m3 (2 to 3 lbs/yd3) of STRUX® 90/40. It is recommended that, in lieu of adding additional water, workability be restored through the use of a superplasticizer or mid-range water reducer. STRUX® 90/40 field experiences reveal the cohesive properties of concrete admixed with ADVA® type superplasticizers are often preferred with STRUX® 90/40 concrete.
STRUX® 90/40 Dispensing and Mixing
STRUX® 90/40 is engineered to have superior dispersion properties when dispensed into concrete in both dry batch and central mix concrete plants. However, the following guidelines should be adhered to so that thorough dispersion and no fiber balling is achieved. It is also recommended that full scale trial batching be conducted prior to job start up.
- STRUX® 90/40 field testing reveals fiber balling can be minimized or eliminated by following the procedures outlined below.
- (Best) Upfront addition of STRUX® 90/40 in concrete ready bags (CRB) into empty drums. NOTE: With upfront addition mode, coarse aggregate batched into front of drum tends to break up fiber balls prior to batching of remaining ingredients.
- (Good) Tail end addition of STRUX® 90/40 in CRB’s into drum revolving at charge speed. NOTE: With tail end addition mode, higher slump concrete tends to disperse STRUX® 90/40 better, compared to lower slump concrete
- (Good) Sprinkle STRUX® 90/40 (out of bags) or place CRB’s on top of the aggregate moving up the conveyor belt
- (Less Preferred) Tail end addition of STRUX® 90/40 into non revolving truck drum
- Central mix plants: add STRUX® 90/40 up front into the plant drum or follow one of the truck dispensing procedures above.
- Truck mixing: ACI 304 4.5.2 recommends 70 to 100 revolutions initially in the yard at mixing speed and an additional 30 revolutions at the jobs site prior to discharge. This is the minimum recommended mixing time for STRUX® 90/40 concrete. If fiber balling is an issue during placement of the concrete, field testing has shown additional mixing at charge speed will help to break up and disperse fiber balls.
STRUX® 90/40 Placing and Finishing
Placement of STRUX® 90/40 concrete should be conducted in a similar fashion to placement of conventional concrete (in accordance with ACI 304, section 5.4.). However, STRUX® 90/40 concrete may tend to be a bit stiffer and want to “hang together” more than conventional concrete. It is recommended that vibratory screeds and/or hand vibrators be used to ease placement of low slump stiffer concrete and assure adequate consolidation is achieved. In addition, testing has shown pumping of STRUX® 90/40 to be similar to conventional concrete.
NOTE: As STRUX® 90/40 addition rates increase, it is critical pump hopper vibrators be in good working order.
During the screeding and floating of STRUX® 90/40 concrete, fibers are likely to remain visible on the surface. This is expected as the majority of STRUX® 90/40 fibers disappear during the power trowel process. Several contractors have successfully used jitterbugs (grade tamper) and/or rollerbugs to assist in pushing STRUX® 90/40 fibers beneath the surface. With broom (and hand) finished surfaces, it should be anticipated that STRUX® 90/40 concrete will still have exposed fibers on the surface after the finishing process is completed.
The power troweling process is the optimal time to work towards achieving a fiber-free surface with STRUX® 90/40 concrete. Field experiences have shown excellent quality finishes (nearly fiber free concrete surfaces) can be achieved by adhering to some or all of the methodologies detailed below.
- Mix proportioning and design includes the use of a superplasticizer and maximum 55% by volume coarse aggregate to total aggregate ratio.
- Conduct power trowel operations as late as possible (near or just after initial set if possible).
- Power float blades, followed by trowel blades should be utilized, with more, rather than less, total finishing on the slab (if possible, continuous finishing once workers and equipment can get on concrete surface).